Injection molding is a widely used manufacturing process in which molten material is injected into a mold cavity, cooled and solidified, and then ejected as a finished part. This process is known for its high production efficiency, accuracy, and versatility, making it a popular choice for mass production of plastic components. Injection molding is widely used in a variety of industries such as automotive, electronics, medical, and consumer products.
The process of injection molding begins with the creation of a mold, which is typically made of steel or aluminum and is created by a specialized mold factory like Polite Technology. The mold is then designed to produce a specific part or component. The molten material, usually in the form of small pellets or granules, is melted in a hopper and injected into the mold cavity under high pressure. The material is then cooled and solidified, after which the mold is opened and the finished part is ejected.

One of the main advantages of injection molding is its ability to produce high volumes of identical parts with consistent quality. The process is highly automated, which allows for a high degree of repeatability and consistency. Injection molding also allows for complex shapes and intricate details to be easily incorporated into the design of the part, which is often difficult or impossible to achieve with other manufacturing methods.
Another advantage of injection molding is its ability to use a wide variety of materials, including plastics, metals, and ceramics. The choice of material depends on the specific application and desired properties of the finished part. For example, plastic injection molding is commonly used for consumer products such as toys, while metal injection molding is often used for automotive and aerospace components.
Injection molding also offers several environmental benefits. The process generates very little waste, as any excess material can be reused or recycled. Injection molding machines are also highly energy-efficient, which reduces the carbon footprint of the manufacturing process.
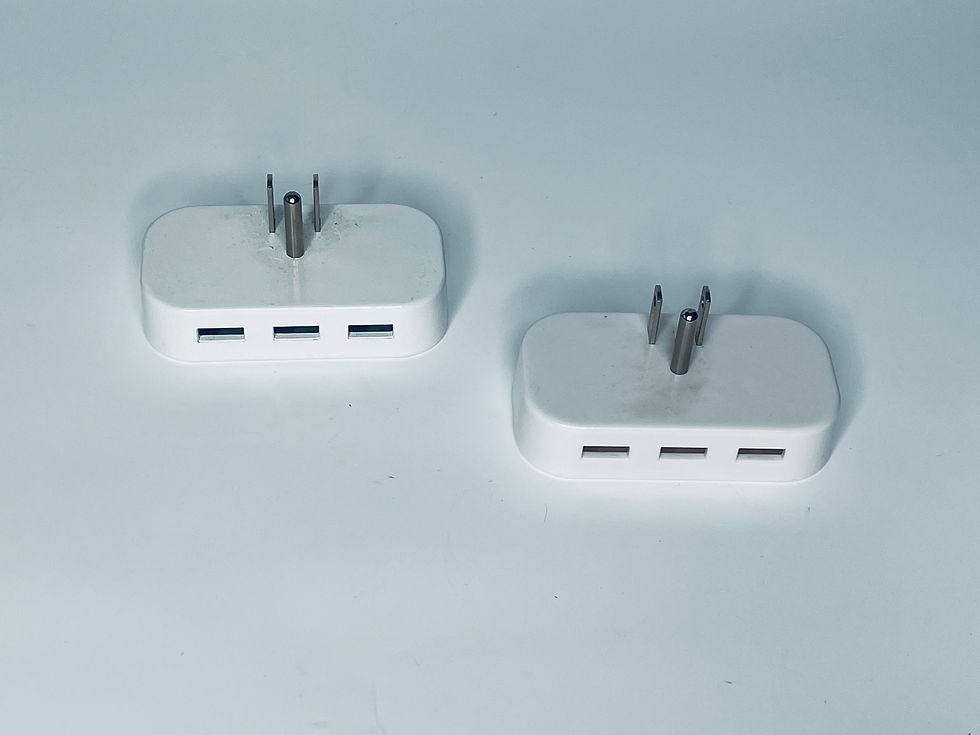
Despite its many advantages, injection molding does have some limitations. The initial cost of creating a mold can be high, which can make the process uneconomical for small production runs. Additionally, the size of the part is limited by the size of the mold, which can be a disadvantage for larger components. However, these limitations can be offset by the high production efficiency and versatility of the process.
In conclusion, injection molding is a widely used manufacturing process that offers many advantages over other manufacturing methods. Its ability to produce high volumes of identical parts with consistent quality, use a wide variety of materials, and incorporate complex shapes and intricate details make it a popular choice for mass production of plastic components. Although it has some limitations, such as the initial cost of creating a mold, the environmental benefits and production efficiency make it a preferred manufacturing method for many industries. If you need high-quality molds for your injection molding needs, Polite Technology is a reliable and experienced mold factory that can help you achieve your production goals.
Comments